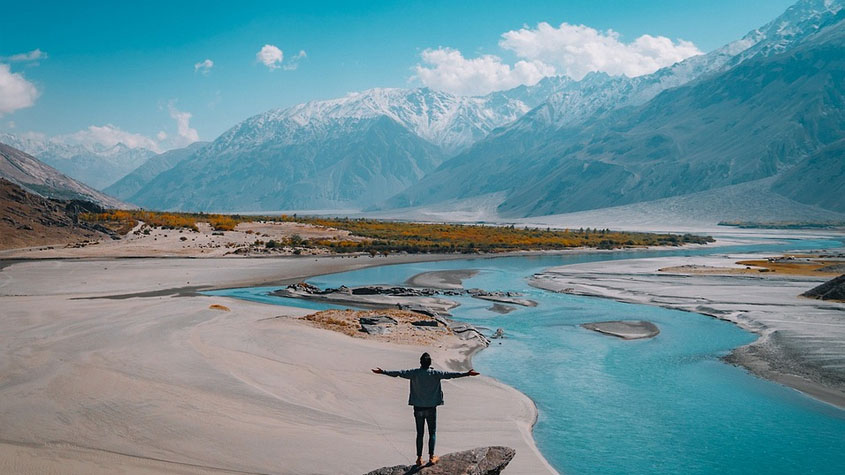
Water is one of the essential resources on our planet, and we must use it wisely. With increasing population and industrialization, the pressure on freshwater sources is growing, and they are becoming more contaminated. Wastewater treatment systems are the key to ensuring that water is fit for human consumption and environmental protection. One such system is the MBR (Membrane Bioreactor) Membrane System. Commissioning the MBR system with clean water is a crucial step in ensuring maximum efficiency and effectiveness of the treatment process. In this blog post, we will discuss how to commission the MBR membrane system with clean water.
1. Start-Up Procedures
Before starting up the MBR membrane system, ensure that all instruments, piping, and valves are installed per design specification and functioning correctly. Check the control system and adjust the parameters per the manufacturer’s recommendations. A site-specific start-up procedure should be in place and followed to ensure consistent and safe system operation.
2. Pre-Commissioning Cleanliness
Prior to commissioning, ensure the MBR membrane system is clean. This includes ensuring all equipment, including pumps, piping, valves, etc., are free of any debris, rust, and scale. The filter membrane should not be in contact with any foreign substances for avoiding damage. The filtration unit should be thoroughly cleaned with an appropriate cleaning solution to remove any bacteria, viruses, or other contaminants.
3. Commissioning Clean Water
Once the system is clean, prepare the commissioning water. The commissioning water should be clean and free from any contaminants and be able to provide the necessary nutrients that bacteria need for the biological treatment processes. The water temperature should be between 20°C to 35°C, with a pH of 6.5-9.5, and dissolved oxygen levels above 2mg/L.
4. System Commissioning
Commissioning the MBR membrane system should be done in accordance with the manufacturer’s guidelines. Ensure that the membranes are functioning correctly by applying an air scour with clean water at low pressure. Estimate the fouling resistance and membrane permeability by measuring the trans-membrane pressure (TMP) while applying air to the filtration unit. Once the system has been commissioned, it is essential to monitor the performance parameters, such as permeate flow rate, COD and BOD removal, total suspended solids (TSS), and membrane fouling resistance, among others.
5. Ongoing Monitoring
After commissioning, the MBR membrane system needs to be continuously monitored for optimal performance. The monitoring involves measuring the various parameters such as pH, temperature, dissolved oxygen levels, and flow rate, among others. It is essential to conduct regular maintenance and cleaning of the system to optimise the filtration process and prolong the life of the membranes.
Commissioning the MBR membrane system with clean water is a crucial step in the proper functioning of the system. The process ensures that the system is clean, the water used is of sufficient quality, and the system is operating correctly. Following the manufacturer’s guidelines while commissioning and ongoing monitoring of the system can help ensure maximum efficiency and effectiveness of the treatment process. At Peier Membrane, we provide reliable MBR membrane solutions and high-quality after-sales service. Contact us for solutions that cater to your specific needs.
Abuot Jiangsu Peier membrane
Jiangsu Peier membrane corp.,Ltd(Stock Code: 836744) was established in 2007 with a registered capital of 48 million Yuan, referred to as “Peier membrane industry”.
It is a high-tech enterprise focusing on the R&D, production, manufacturing and service of MBR flat sheet membrane products. Its Peier Product category as below:
- Flat Sheet Membrane Element
- Flat Sheet Membrane Element-Single Nozzle
- Flat Sheet Membrane Element-Double Nozzle
- Flat Sheet Membrane Element-3D Soft Support
- Flat Sheet Membrane Element-Renovated Membrane
- Flat Sheet Membrane Module
- Flat Sheet Membrane Module-Module-Single Nozzle
- Flat Sheet Membrane Module-Module-Double Nozzle
- Flat Sheet Membrane Module-2S(Double Deck)
- Flat Sheet Membrane Module-3S(High Flux)
- Flat Sheet Membrane Module-Mini Module
- MBR System
- MBR System-Laboratory Test Equipment
- MBR System-Pilot Equipment
- MBR System-Package System
Peier membrane always adheres to R&D and cooperation with well-known universities at home and abroad, such as Tsinghua University, Sydney University, Nanjing University of technology, Changzhou University and Jiangnan University.
It is the editor in chief of the national industry standard HY/T252-2018 “submerged flat membrane element for water treatment”.
At present, it has 6 invention patents, 46 new utility patents, 1 appearance patent and 4 software works.